Quality Control in Manufacturing:
We have a very simple principle when it comes to the quality of our belts and it is followed very strictly.
• Only the very best quality materials are used.
• Every rubber compound has been specifically developed so that PCPL belts out-perform our competitors.
• Every compound batch is quality tested in the laboratory before it is allowed to be used in belt production.
• Every meter of PCPL belt undergoes the toughest quality checks throughout the production process so that the resultant belts adhere to the desired product specifications
The Manufacturing Process:
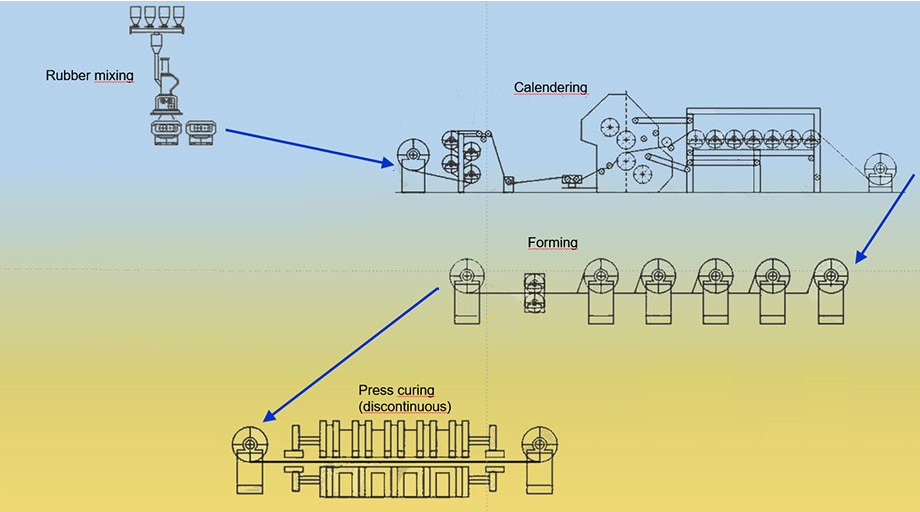
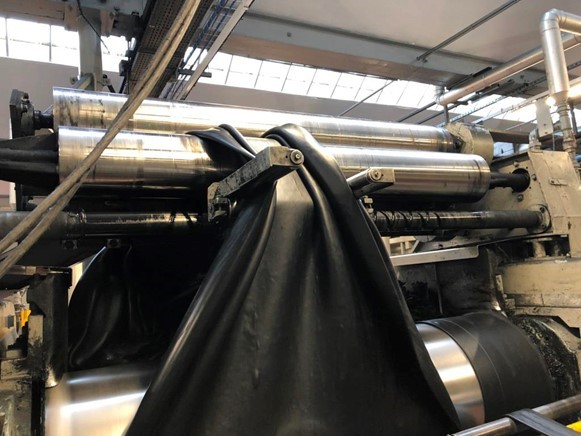
Rubber Mixing and Compounding
Mixing is the first step of the rubber conveyor belt manufacturing process.
Rubber compound is a mixture of a variety of ingredients, but the rubber itself is relatively sticky, and it is difficult to directly mix the various ingredients evenly. It needs to be added to the internal mixer for repeated stirring to be evenly mixed in a particular sequence under controlled process parameters like temperature and pressure.
The rubber mixing process is essentially a process in which the various fillers, curatives, anti-ageing chemicals, and other speciality chemicals are uniformly dispersed in the raw rubber.
During compounding, the rubber molecular structure, molecular weight and distribution, and the aggregation state of the compounding agent all change. Through mixing, the rubber and compounding agents play a physical and chemical role, forming a new structure.
Rubber Calendaring/Sheeting
Calendering is the second process of the rubber conveyor belt manufacturing process.
Calendering is a popular process because of its ability to precisely adjust the product thickness. We use four-roller calendar machine to press the rubber into and press on both sides of the fabric of the conveyor belt to evenly distribute the thickness of the material to ensure that there is no air impurities in the rubber. Important parameters like Tension Control and thickness control are strictly controlled and monitored during the whole process.
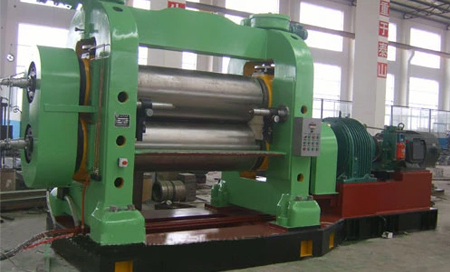
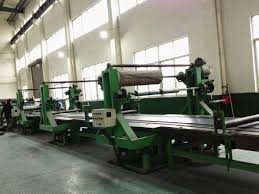
Forming / Building / Confection / Lamination
The semi-finished rubber product obtained by calendering is used to form the required semi-finished product with a cold pressing mechanism according to different specifications. Where in as per specification, the coated fabric plys/layers and rubber sheets from calendar, are placed over each other with even tension to form a composite structure.
Curing / Vulcanizing Presses
Rubber vulcanization is one of the main processes in the processing of rubber conveyor belts, and it is also the last process in the production of rubber conveyor belts.
In this process the uncured Green belt made in Forming is vulcanised using heat and pressure.
At PCPL we use our latest state of art automatic PLC controlled curing presses to ensure perfect finish, uniform thickness and the best mechanical properties in our belts.
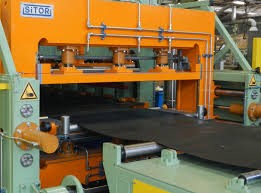